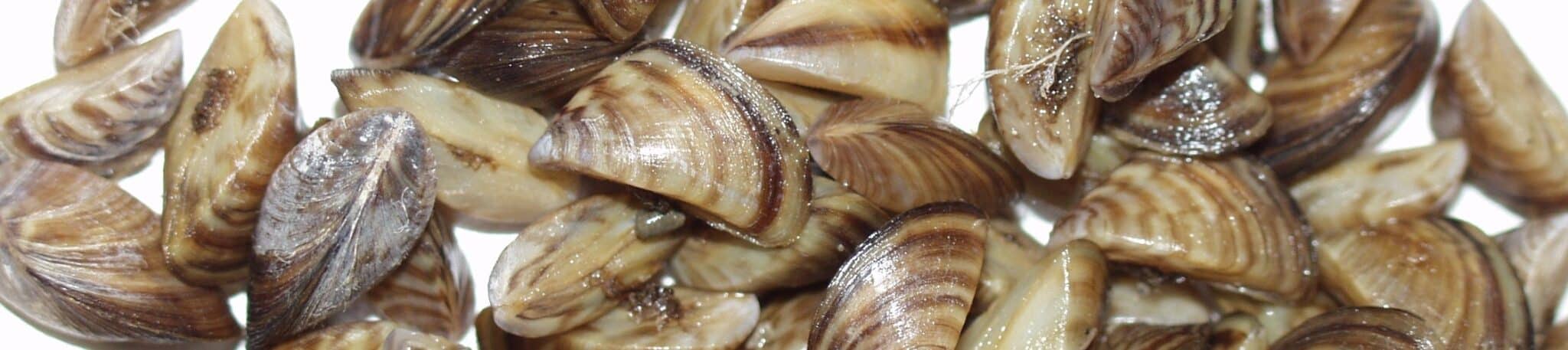
BIOFOULING
COPPER NICKEL SOLUTIONS
Copper use in the marine industry began 200 years ago to resist fouling of naval ships. When corroded, copper forms a protective layer that is toxic to marine like while being relatively safe for humans. The downside of copper is that is slowly wears away and leaches into the surrounding water supply, resulting in deterioration of the alloy and contamination of the water supply. Thus, copper nickel alloy was developed to keep the effectiveness of copper without leaching.
For decades, copper nickel has proven to resist corrosion and zebra/quagga mussel fouling. This alloy retains the effectiveness of copper without leaching into your water source. Elgin offers both a copper nickel coating and copper nickel construction. Our patented coating process (U.S. Patent #5,945,171) utilizes copper nickel alloy and applies it to a stainless steel screen substrate. Compared to copper nickel, stainless steel has double the tensile strength and slightly lower density. This results in a much stronger, lighter, and more cost-effective solution.
Elgin’s copper nickel coating lasts longer and retains stronger adhesion than competing coatings. The superior adhesion is due to the thermal spray process, which is more like welding than painting. While other coatings need frequent re-application, our solutions last the lifetime of the system.
Resources
Case Studies / Videos
Next Steps
COPPER NICKEL OFFERINGS
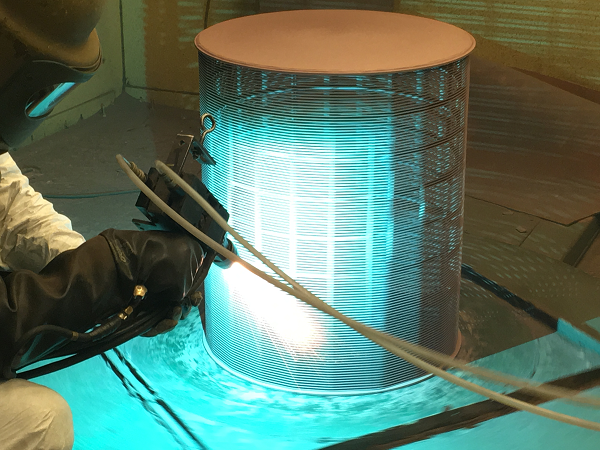
ALLOY COATING
A thin layer of copper nickel alloy is deposited onto a screen assembly or other base substrate. Since copper nickel’s effectiveness comes from its top protective layer (patina) this thin layer is all that is needed to stop the fouling. The devil is in the details of the surface prep and substrate materials required, but after coating this thin layer of copper nickel alloy behaves the same as the base alloy.
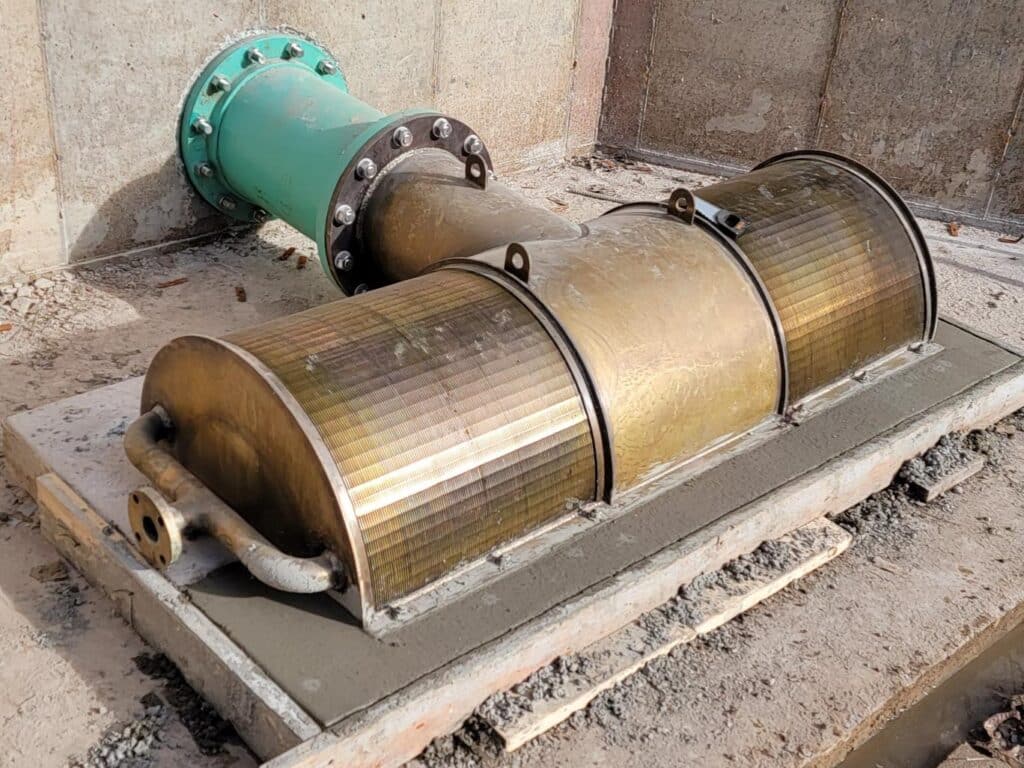